Ford Transit Custom leads class for load-carrying ability
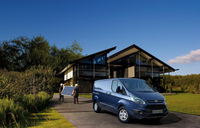
The all-new Ford Transit Custom introduces a new level of load carrying ability to the one-tonne van segment with more space, more convenience and a range of innovative new loadspace features.
Beneath its stylish exterior, the new model remains completely true to its Transit heritage by offering class-leading load volume, together with a carefully optimised load space that delivers outstanding everyday versatility and practicality.
The Transit Custom’s unique new loadspace features were developed by Ford engineers following a special innovation project which captured feedback from customers about those needs that are not currently met by one-tonne vehicles.
“This may be a more stylish Transit, but it’s a more functional Transit, too,” said Barry Gale, Commercial Vehicles chief engineer, Ford of Europe. “The additional features we have built into the loadspace make everyday functions more convenient – so it’s easier for customers to do their job.”
Best-in-class load volume
During the development process, Ford designers and engineers gave maximum priority to combining the largest possible load box within the Transit Custom’s dynamic and streamlined appearance. Particular attention was given to the detailed design of the bulkhead and bodysides to optimise the size and practicality of the load space.
This rigorous approach has ensured that the Transit Custom offers best-in-class load volume:
Short wheelbase (SWB) model – 6.0m3 SAE (full bulkhead fitted)
Long wheelbase (LWB) model – 6.8m3 SAE (full bulkhead fitted)
The SWB model is also the only vehicle in its class capable of transporting three Euro pallets with a one-metre high load, which is also not possible in the current SWB Transit.
The outstanding load carrying capabilities of the van are also reflected in a number of other areas:
Class-leading width between wheel arches of 1390mm allows wide loads to be easily loaded and stored
Class-leading opening height and width of sliding side load doors (1320 x 1030mm) for ease of loading and unloading
Capable of storing large standard 8ft x 4ft (2440mm x 1220mm) boards either vertically at the edge of the bulkhead or flat on the floor
The design of the load box was carefully optimised using detailed CAD models of the load area, and of the items – such as ladders or storage boxes – typically transported by tradesman and professionals, to ensure practicality and convenience in everyday use.
Innovative loadspace features – developed with customer input
The load-carrying capability of the new vehicle has been further enhanced by a number of innovative features which appear for the first time on the Transit Custom.
The new features were developed by Ford engineers as part of a special innovation project which allowed one-tonne van customers to provide feedback on additional capabilities which they would value in the new product.
Having spent time with customers in their vehicles and listened to their input, the Ford innovation team developed product ideas to address the greatest customer needs. Following further customer reviews, the most successful ideas were developed for final production.
The key loadspace innovations in the Transit Custom include:
Load-through hatch in bulkhead enables loads up to three metres in length, such as pipes or ladders, to be safely carried inside a SWB Transit. A hinged opening (596mm x 205mm) at the foot of the bulkhead allows long items to be placed along the floor of the van, and to extend into a secure loadspace underneath the dual passenger seat in the front cabin. LWB models can accommodate loads up to 3.4m long
Deployable integrated roof rack system seamlessly integrated into the roof. The system features three transverse roof bars which are located in recesses in the roof panel, and which can be deployed when required. When not in use, such as when the owner is using vehicle at the weekend, the cross bars can be quickly folded down, reducing drag and fuel consumption, creating a smarter appearance, as well as keeping the vehicle height under two metres for access through car park height restrictions (with the exception of the 330 series). The roof rack is capable of carrying loads up to 130kg
Locking check arms allow the rear cargo doors to be easily locked in place at 90 degrees open, to ensure that the doors cannot be blown around by gusts of wind or passing vehicles while the driver is loading or unloading items
Repositioned tie-down hooks and fixing points located on the body sides. By moving the multiple DIN and ISO compliant tie-downs onto the side wall, the floor is left clear of intrusions or recesses that can reduce usable load area or make complete cleaning of the floor nearly impossible
Easy-clean load floor liner offers enhanced durability and simple cleaning. Similar to the load-bed liner in a pickup truck, the sealed load liner is constructed of immensely strong material, and is tailored to the shape of the load floor, extending up to a height of 80mm around the sides of the load area. Not only is the liner easy to mop or sponge clean, it also protects the steel floor from the possibility of damage during loading and unloading, enhancing residual value
Ultra-bright LED loadspace lighting provides customers requiring brighter lighting within the load box, such as when using the cargo area as a working space, with significantly higher light output from four high-performance LED units
Punishing test regime
From rigorous computer-based simulations, through Ford’s ultra-stringent commercial vehicle test regimes on test rigs and proving grounds, to real-world trials with hard-working customer fleets, Ford’s all-new Transit Custom has been repeatedly pushed to the limit and beyond.
Even before the vehicle goes on sale, it will have been driven the equivalent of three million miles, including at least 250,000 miles with Transit customers.
“The Transit Custom may look stylish and car-like, but that doesn’t mean that we’ve given it an easier time during development and testing,” said Kevin Strutt, supervisor CV durability, Ford of Europe. “The Transit has a hard-earned reputation for bullet-proof reliability, and we’re confident the new model will follow in the same tradition.”
Over 40 per cent of the body is made from high-strength or ultra-high-strength steels while extensive underbody protection means it comes with a 12-year anti-perforation warranty as standard.
The engineering process starts with rigorous analysis of the new vehicle using super-accurate computer-based simulation models, designed to highlight potential durability issues very early in the development phase, so they can be swiftly resolved.
Following the computer-based analysis, prototype vehicles and systems are subjected to testing on proving grounds and test-rigs to Ford’s ultra-stringent commercial vehicle durability standards, which are many times tougher than the equivalent passenger car standards.
The targets are based on real-world analysis of Transit customers to identify the worst-case usage, in a year-long exercise which involved intensive data logging of over 600 vehicles, in seven different markets worldwide, for over six million miles.
The punishing test regime involves at least 30 separate full-vehicle durability sign-off tests which areconducted at Ford’s proving ground facility in Lommel, Belgium, where the conditions range from a high-speed oval, through the toughest rough roads and cobble stones with bumps, potholes and kerbs, to corrosive salt- and mud-baths.
The most rigorous of all these tests is the “Trailer Tow General Durability” which condenses a 10-year vehicle life into an accelerated test that runs 24/7 for six months, towing a fully laden trailer for much of the test. The events and drive routes in this test are correlated to the toughest worldwide conditions, so the vehicle is ready for any global market.
Other extreme tests which the Transit Custom has survived include:
Maximum speed “Autobahn” test simulating non-stop flat-out German Autobahn driving for two months
Low-speed, stop-start city drive cycles to simulate the toughest urban delivery conditions, to prove out clutches, transmission, brakes and the latest Auto-Start-Stop technologies
Various extreme transmission tests such as “shift cycle” and “hot-rod” for the shift mechanism, and the “bump-stop” test that uses aggressive clutch engagement to introduce very high loads into the gearbox
“Figure of Eight” test, which lasts over a month, puts the wheels, hubs, bearings and steering gear through their paces
Front doors were slammed 250,000 times to test for durability