MINI E joins Government electric vehicle announcement
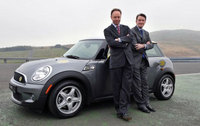
Both ministers drove a MINI E electric car at the event as they announced plans to support motorists by providing help worth £2000-£5000 towards buying their first electric or plug-in hybrid car when they hit the showrooms.
BMW Group has announced that MINI E will go on a twelve-month field trial in Germany and the USA this year, to evaluate the technical and social aspects of living with an all-electric vehicle in a real world environment and plans to include the UK in this programme.
Ian Robertson said, “We believe the MINI E is an excellent vehicle for trialling this alternative form of sustainable mobility. And what better time to do this than in the year we celebrate the 50th birthday of MINI. We look forward to extending our German and American trials to the UK.
“Such a trial cannot be conducted by any single organisation on its own,” he added, “as it goes far beyond the simple test of a prototype electric MINI. To make electric mobility a reality, organisations in both the private and public sectors will need to think differently and act together.”
BMW Group recently applied to the UK Government’s Technology Strategy Board in response to a funding competition announced in December 2008. Proposals were invited for innovative, industry-led collaborative research projects involving ultra-low carbon vehicles.
The UK trial would bring together central and regional government departments, regional development organisations, energy infrastructure providers and academic partners. The common objective is to develop ultra-low carbon vehicles that customers want to buy – and bring them to market as rapidly as possible.
BMW has already established a number of key proposed partners for the UK trial.
Scottish and Southern Energy is the UK’s leading generator of energy from renewable sources and will be installing the private and public charging points required for the MINI E test vehicles.
Academic support will come from the Sustainable Vehicle Engineering Centre at Oxford Brookes University to carry out the data analysis and report the findings.
The MINI E research project supports the BMW Group goal of achieving emission-free driving and underlines its commitment to reducing CO2 emissions without compromising the driving experience. The company aims to begin series production of all-electric vehicles in the medium term as part of the company’s Strategy Number ONE. Know-how gained from the MINI E pilot projects around the world will play an important part in informing future strategic and technological decisions.
At the end of the one-year trial a comprehensive report documenting the main findings of the MINI E research project will be published. This will help inform those organisations seeking to create the political, technical and commercial framework necessary to enable sustainable mobility in a low carbon future to become reality.
The BMW Group is the most sustainable car company in the world – as the latest Dow Jones Sustainability Index (DJSI) recently confirmed for the fourth year in succession. The company already offers the most efficient cars in the premium segment, thanks to Efficient Dynamics technologies. The BMW 118d was named World Green Car of the Year 2008 and the Hydrogen7 has already made CO2-free driving a reality.
MINI E specification and performance
The MINI E’s electric drive train produces a peak torque of 220 Nm, and power is delivered to the front wheels via a single-stage helical gearbox. This unique engine and transmission arrangement powers the MINI E seamlessly to 62 mph in 8.5 seconds and on to an electronically-limited top speed of 95 mph.
Based on the current MINI Hatch, the car is available as a two-seater. The space normally inhabited by rear passengers is reserved for a lithium-ion battery.
When in use in the zero-emissions MINI E, the battery unit combines high output with ample storage capacity and remarkable power output. The lithium-ion storage unit will have a maximum capacity of 35 kilowatt hours (kWh) and transmit energy to the electric motor as direct current at a nominal 380 volts. The rechargeable battery is made up of 5,088 cells grouped into 48 modules. These modules are packaged into three battery elements that are compactly arranged inside the MINI E.
The energy storage unit’s components are based on technologies proven in power supply units for mobile phones and portable computers. The MINI E’s lithium-ion battery can be plugged into all standard power outlets. Its charge time is strongly dependent on the voltage and amperage of the electricity flowing through the grid. As with existing research projects in the USA and Berlin, users can recharge a battery that has been completely drained within a very short period of time using a wallbox that will be supplied as standard with every MINI E. With 240V/32A, charging time for the car will be around four hours. There is also an intention to establish a network of public charging stations.
The wallbox will be installed in the customer’s garage, enable higher amperage, and thus ensure extremely short charging times. Wallboxes fully recharge batteries in just two-and-a-half hours. Only lockable garages or similar buildings will qualify as suitable power stations for the MINI E.
Driven by electricity: zero emissions at minimal cost
A full recharge draws a maximum of 28 kilowatt hours of electricity from the grid. Based on the car’s range, a kilowatt hour translates into 5.4 miles. Besides the benefit of zero-emissions driving, the MINI E thus offers significant economic advantages over a vehicle powered by a conventional internal combustion engine. Fully re-charging the battery using off-peak electricity at current prices will cost around £1.50. Using higher-rate daytime electricity, the cost will still be less than £4.00.
The heavy-duty battery delivers its power to an electric motor, which is mounted transversely under the MINI E’s bonnet. This power unit is able to unleash its full thrust from a dead standstill and is complemented by its dynamic deceleration potential, which is directly coupled to the accelerator pedal.
As soon as the driver releases the accelerator pedal, the electric motor acts as a generator. This results in braking force and the power recovered from the kinetic energy is fed back to the battery. This ensures a comfortable and smooth driving experience. In city traffic, some 75 per cent of all deceleration can be done without the brakes. Making substantial use of this energy regeneration feature extends the car’s range by up to 20 per cent.
The MINI E’s brake system comes with a newly developed electric pump. Its Electrical Power Assisted Steering (EPS) is the same as the one used in series-produced MINIs.
The MINI E’s 1,465 kilograms is evenly distributed across the car. Modifications to the suspension system and the car’s Dynamic Stability Control (DSC), adapted to the car’s specific wheel loads, ensure safe and dynamic handling, typical of MINI.
Unique styling to mark out the new MINI E
Every MINI E produced for this pilot project will have the same paintwork and bear a serial number on the front bumper.
The MINI E’s coachwork is painted metallic Dark Silver on all panels but the roof, which is coloured Pure Silver. A special MINI E logo depicting a stylized yellow power plug in the shape of an “E” set against a silver background appears on the roof, front and rear wings and the charge point cover. The dashboard trim, and the door jamb, feature the same logo in slightly modified form. The colour of the roof edges, door mirrors, interior styling accents and seat seams will match the yellow of the “E” logo.
Inside, the central gauge and battery level indicator behind the wheel of the MINI E - which replaces the MINI’s rev counter - feature yellow lettering against a dark grey background. The battery level is displayed in percentage figures. The central gauge includes an LED display indicating power consumption in red and power recuperation in green.
Production in Oxford and Munich
The MINI E has already gone through the major phases of product development for series-produced vehicles and passed numerous crash tests on the way. The MINI E’s energy storage unit emerged completely unscathed from all of the crash tests mandated by European standards.
Production of the 40 cars for the UK trial will take place shortly at the company’s Oxford and Munich sites and is scheduled for completion before October 2009. MINI’s Plant Oxford will be responsible for manufacturing the entire vehicle on the standard production line, with the exception of the drive components and the lithium-ion battery. The vehicles will then be transferred to a specially equipped manufacturing facility situated on BMW plant premises in Munich where the electric motor, battery units, performance electronics and transmission will be integrated.