3 industries that benefit from injection molding
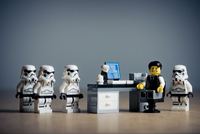
Injection molding is the most common method for mass-producing plastic products. With the right material and blueprint, you can produce anything from lawn chairs to toys or disposable cutlery.
As such, the technique is extremely popular across industries and provides small businesses with a cost-effective way of freeing the manufacturing process from the big companies. Furthermore, injection molding opened the door to innovation and creativity, which can only be beneficial for everyone involved.
However, some domains get greater benefits than others, so today we are going to talk about the top 3 industries that are boosted by this manufacturing process.
#1: Toys
Did you know that your favorite building blocks (aka LEGO bricks) are made using plastic injection molding?
The same is true for many toys nowadays. In fact, we wouldn’t have Captain America or Iron Man figurines if it wasn’t for this technique! Most modern toys are produced this way, but the technique also opened the door to a higher degree of customization. As such, due to injection molding, we now have businesses that can create unique toys, made after specifications received from customers (personalized figurines, toys after kids’ drawings, and more).
The fact that injection molding is great for creating small pieces without too much effort and energy is the main reason why the toys industry reaps the most benefits. Melted plastic is malleable enough to create small objects with intricate decorations, that are also durable.
There is even a small B2B sector, where toy creators can partner up with companies that have the manufacturing technology. Creators order custom-made parts online, receive an injection molding quote based on their project’s specifications and start a collaboration.
#2: Electronics
Every piece of electronics in your house has some plastic in it. It can be anything from a case, a frame, or some type of support. The main purpose of these elements is to provide protection (for both the user and the device) and enhance the aspect and use of the device.
And, you’ve guessed it, most of these plastic elements are made using injection molding. The production method is fast, efficient, and smooth, which is why it’s been integrated into most electronics factories around the world.
#3: Medical & Dental
Items produced for the medical and dental industries must respect strict standards of safety and quality. The same goes for the disposable items (like sample cups, jars, vials, and more) and tools that must be made from plastic (forceps, tubing, clips, and more).
Injection molding is perfect in this situation as it allows for one-piece items that don’t have nooks and crannies where bacteria and viruses could gather. It also allows producers to keep the manufacturing costs low while providing high-quality items.
Wrap Up
As you can see, we use plastic injection molding in a wide range of industries, from toys to medical equipment. This is because plastic is such a versatile and easy-to-work-with material. However, it is not extremely durable, which means that other industries are forced to use different methods like CNC manufacturing.
Still, since it was invented, the injection molding technique helped change our lives for the better.