Volvo Trucks cab factory to be entirely CO2-neutral
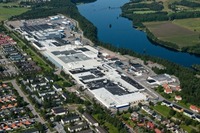
In conjunction with the meeting of the European Ministers in Umea, Sweden on October 14-16, Volvo Trucks showcased its highly successful pro-environmental work at the cab factory in Umea. For several years now, the company has been making major investments in improving the efficiency of its energy usage and the goal is to have a carbon dioxide-neutral factory with locally produced energy within a couple of years. Energy consumption has decreased by 30 percent per manufactured cab over the past ten yeas, at the same time as there has been a record increase in production volumes.
Umea’s green focus echoes Volvo Trucks’ over-riding environmental goals, which among other things means that all the company’s large production plants are to be CO2-neutral by 2010.
“For us, Umea is a shining example and a symbol of our environmental commitment. The factory has for many years worked very successfully with environmental issues, generated highly innovative solutions and shown in concrete terms that this commitment benefits both the company and the environment,” says Lars Martensson, environmental director at Volvo Trucks.
Halving of propane consumption
Today 90 percent of the factory’s energy consumption is renewable. The target is 100 percent. Of the 106 GWh of energy that the Umea factory consumed in 2008, 13 percent still consisted of propane, even though propane consumption has been halved compared with 2006. The propane used for the painting ovens has been replaced with district heating and today propane is the only fossil fuel being used. The district heating system has also replaced oil as a fuel, and all told emissions of CO2 have been cut by 8000 tonnes a year. Today energy is recycled to the tune of 80 GWh per year. Now propane is being replaced by DME produced from biomass. This is taking place in a joint project bringing together Umea University, Umea Energi, Ö-vik Energi and Volvo Trucks.
“The DME project is a good example of how research, business and society work smoothly together to find solutions that really work,” continues Lars Martensson.
Cooling from an icy underground river
The most spectacular energy saving is seen in the factory’s cooling system. Close to the Ume River and the Volvo factory there is an underground ice river that maintains a constant cold temperature come summer or winter. The icy water from this river is pumped via a two kilometre long pipe into the factory’s own system. This water is used in various cooling systems and has replaced many of the cab factory’s refrigeration plants which otherwise used cooling agents such as freon. The biggest consumer of cooling water is the dehumidification of the air that is fed to the paint-boxes in the paintshop. The first supply of ice-river water reached the factory about a year ago, and its cooling effect corresponds to 3000 kilowatts.
The world’s cleanest paintshop
Work on reaching the environmental targets has also prompted energy savings and environmental improvements in the factory’s paintshop. The paintshop has been modernised and production has been streamlined in several stages, thus also cutting the consumption of paint and solvents and slashing emissions to the surrounding air. In 1988, solvent emissions to the air were about 70 grams per square metre of cab surface. Today emissions are below 10 grams, which is way below the EU’s limit of 55 grams per square metre.
“We are now the world’s cleanest paintshop as regards emissions of solvents to the air, and it is our aim to maintain this lead in the future too,” says Anders Olausson, plant director at Volvo Trucks in Umea. “We intend to continue our drive to be even regarding both environment-impacting emissions and energy consumption. We can see that what we’re doing is good for the environment, and also that it leads to better production economy for us,” he concludes.