Volvo’s test rig simulates a truck’s lifetime in just a few weeks
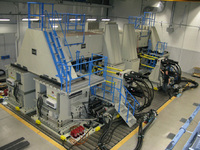
A truck’s axles are subjected to immense stress and strain every day, year after year. To ensure they are rugged enough to withstand the toughest situations without having to over-dimension them, Volvo Trucks is using an entirely new test rig for wheel axles in its product development.
Located at Volvo’s facility in Gothenburg, Sweden, the new test rig is the largest of its kind in the world and is and can handle full-scale tests of axle assemblies up to 32-tonne bogies, making it unique in the truck world. In the space of a mere few weeks, it can simulate the stresses and strains that truck is subjected to throughout its entire lifetime. Equivalent tests took four times longer in the previous test rig.
“The tests that we can now perform in six to ten weeks with the new rig used to take six to eight months and involved testing the vehicles out on the track. The new rig also gives us better-quality test results,” says Göran Johansson, manager of test operations at Volvo.
Quality assurance is a crucial and time-consuming part of Volvo Trucks’ development and quality work. The entire product development phase has been shortened since important test operations can be conducted in just weeks instead of months. In the new test rig, it is also possible to carry out more advanced tests early in the product development cycle. The tests are one stage of product development for next-generation axle assemblies designed to optimise the vehicle’s all-round construction.
“Optimisation is all about ensuring that customers can depend on the truck’s various systems always functioning correctly, while simultaneously ensuring that the systems do not weigh or cost too much due to over-dimensioning,” explains Göran Johansson.
Complex simulation of reality
To succeed in this equation, it is necessary to be able to test the various systems in complex cycles, and with considerable precision. In Volvo’s new test rig, the entire axle assembly is subjected to vertical and horizontal forces as well as torque applied to the wheels. All this force and torque can be simulated individually and simultaneously. During the course of the test, input data can be gathered from more than a hundred measurement points. To achieve the required degree of simulation precision, the parameters in the test rig’s control electronics can be updated more than 1,000 times a second.
The tests are run in real time; the axles are subjected to the same stresses and strains that occur in daily truck operation, only far more frequently. There are several basic programs for the various test cycles – long-haul, distribution operations and construction duties. Furthermore, the test cycles can be individually tailored for special driving conditions within each respective transport segment.
The various test programs are based on the readings obtained from customer vehicles driven on the test track.