Tarmac pioneers unique DAF-based low-weight mixer
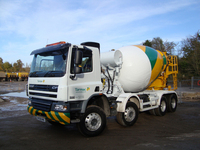
The combination of DAF’s low-weight FAD CF75 four-axle chassis and an eight cubic metre McNeilus Revolution composite drum, designed and made in the USA, has resulted in a mixer that is as much as 600 kgs lower in weight than one with a conventional steel drum, weighing in at just 12,200 kg.
This low unladen weight will help operators to stay within the legal maximum of 32 tonnes whilst carrying a full eight cubic metres of cement. It can be difficult to keep an eight-wheeler fitted with an eight cubic metre mixer within its legal gross weight and a common safeguard against overloading is to reduce the load by as much as half a cubic metre. This new solution results in a mixer that can operate to its full capacity and stay legal.
The DAF based mixer is being trialled by Tarmac and is being operated by their contracted haulier John Smith, who is running it out of their batching plant at Stancombe near Bristol. The trials are being undertaken with the support of key Tarmac supply partners DAF Trucks, dealer Greenhous DAF, and mixer specialists McPhee Bros of Glasgow.
“We expect the trial of this vehicle will demonstrate a number of benefits,” says Lee Green, Category Manager at Tarmac. “The DAF can carry a full load of eight cubic metres and do so within its maximum weight limit. This not only makes it easier to stay legal on weight, but also could represent a payload increase of as much as 10% when compared to a typical four-axle mixer with a steel drum.
“Fuel efficiency could be improved too, as when running empty on return trips the overall vehicle weight is lower. The DAF CF75 eight-wheeler, and particularly its cab, gives us a good low-weight platform onto which to fit the Revolution drum and this adds to the overall weight saving and fuel economy.”
Makers McNeilus claim that the use of composite materials helps to reduce cleaning times, which would improve turnaround times between loads. Service life could also be extended to as much as twice that of an equivalent steel drum and maintenance could be reduced. McPhee Bros say that this is because eight cubic metre steel drums are often manufactured out of 4mm steel in order to reduce weight and the blades and skin are likely to need replacing more frequently than the harder wearing composite materials used in the Revolution drum.
Another environmental benefit is that the noise level of the Revolution drum is markedly lower than a steel drum, largely due to the smoother running of composite materials. These also have better thermal properties that enable the drum to maintain slump for longer in extreme temperature conditions. The reduced amount of torque needed to turn the Revolution should also help improve fuel economy.
Tarmac’s new DAF is powered by the 9.2 litre PR engine rated at 360 bhp (265 kW) giving a comfortable 11.25 bhp per tonne of power to weight at its maximum laden weight. Tarmac has chosen to go to the Euro 5 emissions standard, which is achieved through the use of SCR technology.