Suckling Transport joins ‘Driving for Better Business’
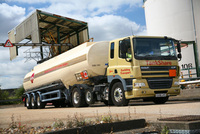
Fuel tanker operator Suckling Transport is on the road to achieving its goal of zero road incidents after recording huge falls in the severity and frequency of crashes, while simultaneously improving fleet efficiency and winning business.
The Essex-based company operates a fleet of eight company cars and 65 tankers, which deliver almost two billion litres of inflammable liquid per year across the UK from 10 oil terminals to filling stations and other commercial delivery points.
The fleet travels approximately 9.5 million kilometres (six million miles) a year and since launching the Zero Incident Project two years ago, Suckling Transport has witnessed a 76% decline last year in the severity of accidents with the frequency of accidents falling from an average of 6.12 per one million kilometres of the previous four years to 2.88 in 2009. That reduction resulted in a 14% insurance premium decrease this year.
It is that record of achievement that has seen Suckling Transport, which is a signatory to the European Road Safety Charter, to join the Government-backed ‘Driving for Better Business’ campaign, which is managed by RoadSafe.
Suckling Transport, which has won a string of industry awards for its approach to occupational road risk management, is the campaign’s 51st ‘business champion’. They are used to promote the financial, legal and moral benefits of occupational road risk management to public and private sector organisations across the UK.
There are an estimated up to 200 road deaths and serious injuries a week resulting from crashes involving at work drivers, and more employees are killed and seriously injured on Britain’s roads while driving on behalf of their employer than in any other work-related activity.
Suckling Transport is an independent organisation whose approach to road safety is championed by managing director Peter Larner. He said: “The company competes in a market sector dominated by large, multi-national companies. To compete successfully, we must differentiate ourself and road safety seems to be the perfect way to do this.
“Road safety saves money as well as lives. Training is seen by the workforce as career development not punishment. Meanwhile, benchmarking our performance against other organisations demonstrates the benefits of that training and drivers now see this as enhancing their skills, rather than imposing compliance of the rules.
“Future short-term developments revolve around our continued journey towards zero incidents. Maintaining zero status once we get there will rely on preventative skills and the co-operation of the workforce in identifying potential risks and near miss incidents.
“My role is to create a robust safety culture that is understood, and contributed to, by the workforce. It has become a generative safety culture, based on a consensual ethos, rather than prescription and is subscribed to by the workforce, rather than imposed on employees.”
Road safety initiatives introduced as part of the company’s Zero Incident Project, which also covers the company car fleet, include:
A drivers’ handbook issued to all employees who also have access at each terminal to the Site Route Risk assessments and details of safe parking areas on route through the company’s ‘Safe Havens’ information, which identifies safe parking areas for drivers.
Site and route risk assessments for every address tankers deliver to.
A ban on all mobile phone use, including hands-free, while driving.
Frequent DVLA driver licence checks.
Directions to manage driver fatigue. While tanker drivers are governed by the European Union drivers’ hours regulations, company car drivers are advised to prevent tiredness - a major cause of road crashes - by taking a break after two hours of driving; take into consideration their work load undertaken before and after the journey; and if the total working day exceeds 12 hours must plan for a night away and make accommodation arrangements
All employees being medically fit to drive including not being under the influence of prescribed or recreational drugs and anyone who has been drinking alcohol within the previous 12 hours must consider whether they are fit to drive. Random drug and alcohol tests are conducted.
Company car drivers completing a pre-start vehicle check which covers: fuel, water and oil levels; tyre pressures; the efficient working of lights and windscreen wipers.
The creation of a team of six driver instructors - drawn from the workforce - who assess employees’ driving skills at least once every two years but, more frequently, where a requirement for intervention training is indicated by on-board computers fitted to tankers.
The use of Virtual Risk Manager software during the driver recruitment stage to produce a short-list of applicants who then undertake an in-cab driving assessment. All newly recruited drivers undergo a minimum of one week’s training alongside a driver instructor
Journey management checks are conducted by managers to ensure drivers are adhering to speed limits and not recording rest breaks whilst delivering.
Vehicles are now fitted with on-board computers which produce reports to identify any workforce driving skills shortages with remedial training then taking place.
Driver toolbox talks held with managers conducting behavioural safety observations of drivers at work.
Regular safe driving communication through quarterly news bulletins, a monthly ‘Safety in Numbers’ newsletter and, more formally, through health safety and environment committees.
In addition, Suckling Transport’s two main customers, Shell UK Oil and ConocoPhillips, conduct annual audits of its safety systems, while the Freight Transport Association conducts a 100% analysis of drivers’ tachograph charts for compliance and also completes a Working Time Directive check.
Meanwhile, staff formed focus groups and conducted cold case reviews of past incidents, enlisting the help of suppliers to identify any new technology that could have prevented those incidents. That led to the launching of 14 separate initiatives to test features that could be added to vehicles including object sensors, reversing aids and lane departure warning system.
Additionally, trials are currently being conducted on new software that will automatically check for speed compliance with the road limit on which tankers are being driven.
To encourage staff to pro-actively focus on safety, drivers are incentivised to produce potential incident and near miss reports to identify risks before accidents occur. Last year, 337 such reports were submitted.
Mr Larner said: “Every accident, near miss, or potential incident is an opportunity to improve safety. The benefits of our Zero Incident Project are multiple and include a significant reduction in vehicle downtime, improved fleet and fuel efficiency, a reduction in driver turnover and improved relationships with our customers contributing to new contract wins with both Shell UK Oil and ConocoPhillips.”
Looking to the future, Mr Larner is already planning the next manager safety project that will see the creation of the ‘Suckling Village’.
He explained: “Customers, suppliers, group companies, employees and employees’ family members are all part of the ‘Village’. By sharing our best practice with others we can learn from their best practice. The bigger the ‘Village’, the greater the challenge but it will help Suckling Transport achieve a completely safe environment for our workforce and everyone connected with the business.”
‘Driving for Better Business’ campaign director Caroline Scurr said: “Suckling Transport is great example of good leadership in a small business. The hands-on approach by the company’s managing director is exactly the type of occupational road risk management and leadership that we encourage in business.
“Suckling Transport has recognised that road crashes can be hugely disruptive to its business and the well-being of staff. The implementation of a wide range of safe driving initiatives has triggered major benefits that other public and private sector fleets, irrespective of their size, should adopt.”